
Removing and inserting the card and then refreshing has no effect. SD card is working one minute, and then it no longer works until a power cycle. As a result I'm using the SD card only now. My printer is 10 feet from my WiFi router. Sometimes the connection will just drop randomly and not coming back for minutes at a time.

I have to restart Up Studio 3 to get it to come back. selecting filament type) makes it lock up and frequently force close. Wifi seems to be crazily unreliable on this printer. Wifi drops all the time and Wand server force closes I've also checked and re-seated the black FFC ribbon cable to the X-axis stepper assembly, but the problem remains. Prints are at standard speeds and settings. Not excessively hot, so it doesn't seem to be overworked. I've checked the stepper temperature with a FLIR camera and to the touch - it's about 45C when this happens. This can be "resolved" in one of two ways: Power cycle the printer, at which point the X-axis comes back to life, or go into Information and hit Reset to reset the printer. The picture below shows the result of this - the horzontal mess closest to the camera is when it stopped working and the one further back is where I moved the X-axis out of the way by hand to see what was going on (the white stuff on the build plate is gluestick residue). The extruder head can be moved by hand freely while the Y-axis and Z-axis continue to function. Mid-way through the print, at a random time, the X-axis just gives up the ghost and stops working. This has resulted in failed prints for each of the fourteen prints I've attempted on this printer so far. X-Axis stepper gives up mid-print, every print I suspect I have a hair-trigger sensor - I get a flash of the red LED on acceleration and deceleration of the head, or even with the lightest of touches in any direction with my finger. I then removed and reseated the extruder head and subsequently got wild results, until I gave the head a gentle knock and it went back to normal. Cables are out of the way and unfouled.Įdit: On a hunch, I removed the filament and feed tubes from the extruder and got more consistent results. There are no stray bits of plastic on the bed. The end of the nozzle is clear of filament. Everything is tightly fastened and secured. I'm not sure why this is the case, except to suspect that the strain guage method of detecting contact with the bed is inaccurate. You can see the results of seven sequential runs here: On the wonky 2mm-out runs, measurement point 10 barely moves the Z-axis down before registering a hit. Each time I perform auto calibration I get one of two results: something sane or something about 2mm out with a single zeroed value (measurement point 10). I have manually levelled the bed as instructed, initialised the printer, and then performed auto calibration. I am getting endlessly inconsistent results of auto calibration. two mainboards fried in the same place, according to a post on the Tiertime new forums). I'm curious to hear if anyone else has experienced similar problems or any other type of issue? (e.g. As a result, this printer is completely unusable. Unfortunately I've experienced fundamental problems with the Cetus 2 that have resulted in failed prints every single time. As a happy owner of a modified Cetus3D MkII I had high hopes for this printer. (FWIW, my main issue was weird Z-heights, where say a 30mm tower would print like 2mm too tall.I received my Cetus 2 a couple of days ago and installed it today.
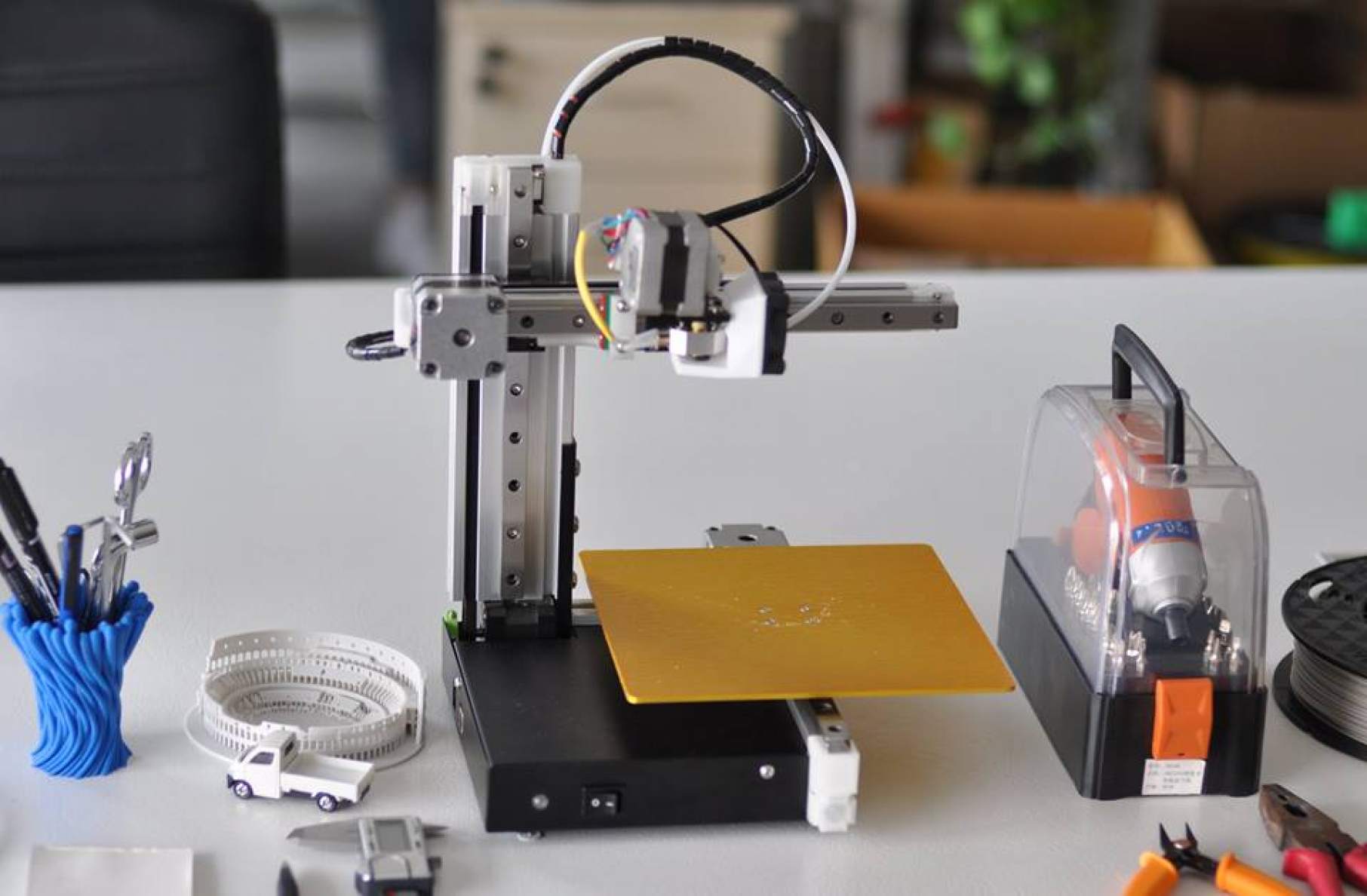
#Cetus3d x axis software
I’m curious if you get this to work-I gave up on Simplif圓D because it wasn’t worth fighting with such an expensive software package, but having Cura as an alternative would be nice on certain prints. I also used just a single M109 command to turn the extruder off at the end.
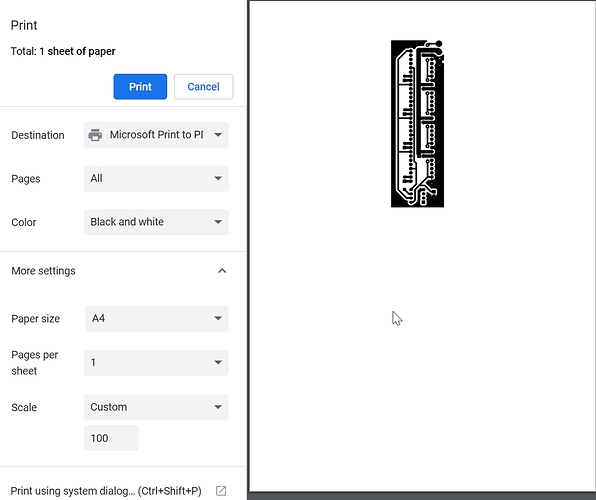
#Cetus3d x axis code
In Simplif圓D, my only heater-related command in my start code was this: M109 S wait for extruder temp to stabilise I’m not sure why that would cause your heater to keep running, though. From here, it seems like the difference is that M109 “blocks” and waits for the temp while the M104 lets the script continue. The biggest heater-related difference I see between your start script and mine is that you’re using multiple M104 and M109 commands, while I only had a single M109. I had 99 problems but a runaway heater wasn’t one. I’m no expert, but I fought with my Cetus and G-code for a few weeks (by way of Simplif圓D). G1 Y20 E2500 F500 Extrude 25mm filament over 90mm Y axis G0 Y10 F500 Move 10mm to get rid of material
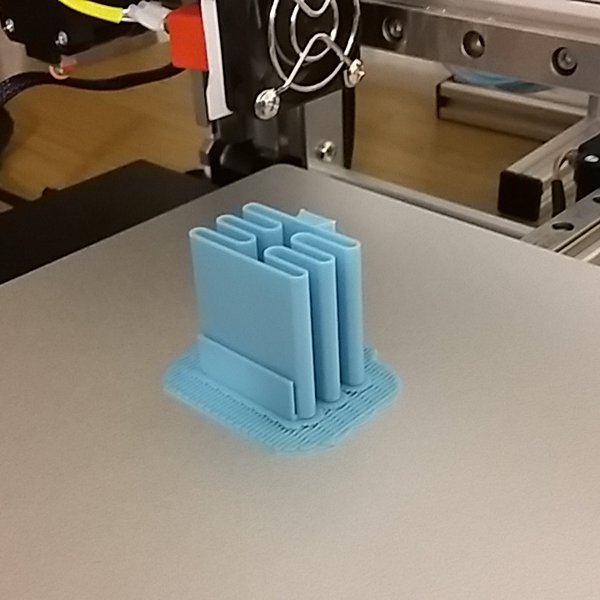
G1 X2 Y178 F5000 move to back right corner Even when it is completely done with the code. The problem is that, instead of maintaining my print temp, it keeps heating up. So far I have a working start and end sequence.
